Predictive maintenance with IoT at ERIKS
Early and preventive maintenance prevents downtime of machines or even entire production processes. Conclusion developed an independent IoT platform for industrial service provider ERIKS. ERIKS can connect its high-quality mechanical engineering components to this as well as monitor them. Both the users and ERIKS itself benefit from this: the platform facilitates predictive maintenance and detecting faults at an early stage. The Total Cost of Ownership falls, and continuity is guaranteed.
Client
ERIKS
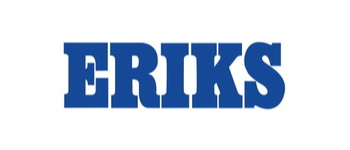
Market
Industry
Theme
Emerging technologies
Date published
1 februari 2021

Innovating with predicitve maintenance and IoT
ERIKS Nederland is an experienced industrial service provider with a single mission: to make companies better and more efficient. To this end, ERIKS supplies high-quality mechanical engineering components to over 200,000 customers worldwide together with an extensive maintenance and repair programme. Future-proofing is not an empty slogan for ERIKS: by researching and embracing new technologies, ERIKS helps its customers to innovate, excel, and exceed expectations. The IoT platform that Conclusion developed for ERIKS is an example of this. This makes predictive maintenance on mechanical engineering components possible.
Condition based maintenance
The IoT platform fits in perfectly with ERIKS’ concept of condition-based maintenance: measure and take stock of the condition of your asset and carry out maintenance when the condition of the asset demands it, before failure occurs. Here’s one example: predicting maintenance of large excavators for ERIKS customers. Sensors indicate the status of such a machine based on lubricant levels. This makes it possible to predict and efficiently schedule maintenance or repairs in the work schedule. This ensures that such maintenance or repairs do not come as a surprise during busy projects, which would result in a loss of income.
Bridge between machine and cloud
In developing the IoT platform, the biggest challenge was sending local sensor data from the excavator's electric motors to a dashboard running in the public cloud. For this purpose, Conclusion developed an Edge solution in combination with a digital twin in the cloud. The Edge computer is in the workspace and bridges the gap between machine, sensor, and public cloud. The data from this Edge solution is stored in a digital twin model in Microsoft Azure and shown on a dashboard created in Mendix. This allows the operator and the planner to see the performance of the electric motors. Anticipation is based on graphs of deviations. In case of impending disruptions, timely intervention is possible.
“The biggest challenge is sending local sensor data to a dashboard that runs in the cloud. To do just this, Conclusion has created an EDGE solution for us. The computer is in the workspace and bridges the gap between machine and the cloud.” Says Tim Noordhoek, CTO at ERIKS Digital.
Total solution with a single dashboard
A special feature of the platform is its brand independence. This means that ERIKS can connect both its own brands and its multi-brand machines to it. In other words, it is one dashboard for the entire product range and is independent of product suppliers. This also offers interesting perspectives for the future, for adding powerful components, such as analyses and algorithms. This will not cause any inconvenience to the rest of the chain or equipment.
“There are many providers of IoT solutions, but these are often tied to a single product vendor. All suppliers can be connected to our dashboard.” Says Tim Noordhoek, CTO at ERIKS Digital.
Optimal utilization of the production line
This application of IoT offers economic advantages. A customer who continuously monitors their equipment can prevent their production line from coming to a halt while also minimizing failure costs. They can even increase production by reducing the need for manual checks. This can go even further in the future when ERIKS starts using algorithms based on all the experience it has gained. In this way, ERIKS continues to work on its futureproofing. This applies both to its customers and to itself.
Conclusion
Conclusion serves its clients through our unique ecosystem of IT and business oriented companies. Each one is an authority in its field. By deploying such expertise in a targeted manner, we work to help clients become resilient, agile, and distinct. In this client case, these two business units play a leading role: AMIS Conclusion and Conclusion Low Code Company
AMIS Conclusion
With Conclusion Connect, AMIS Conclusion is the specialist in linking the physical world - of engines, meters, pumps and industrial installations - to the digital world on a large scale. They focus on getting maximum return on the investment in cloud technology. Rapid business impact is paramount. As such, AMIS Conclusion provides for higher customer satisfaction, a higher utilization of companies’ machine parks, lower costs for maintenance, and higher availability.
Conclusion Low Code Company
The creation of the screens and dashboard for the IoT solution in Mendix was done by Conclusion Low Code Company. In addition, they developed a mobile Mendix application for ERIKS to replace the paper-based service management process for checking steam traps. Offline functionality was a requirement for this steam application, as many industrial plants do not – or should not – have an internet connection. By using an agile approach, a first version or Minimal Viable Product (MVP) was quickly created in close collaboration with ERIKS. This version was used to gain experience in the field. Based on the experience of the service engineers, functionality was added in several sprints, for example the option to read QR codes and the storing of the GPS data of the steam traps.
Want to know more about what IoT can do for your organization?

Robbrecht van Amerongen